How Defoamers Improve Efficiency in Manufacturing and Production
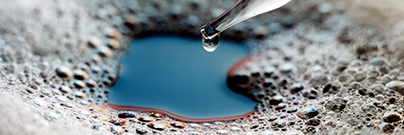
Comprehending Defoamers
Defoamers play an important duty in various making procedures by effectively combating the formation of foam, which can interfere with procedures and affect item top quality. Foam can arise in various contexts, such as during blending, home heating, or chain reactions, potentially resulting in ineffectiveness and incongruities in items. The mechanism whereby defoamers run usually entails lowering the surface area stress of the liquid, allowing bubbles to increase and integrate to the surface area extra conveniently, where they can after that rupture.
Reliable defoamers not just reduce foam development however also keep compatibility with the product, making certain that there are no adverse results on the final result. Understanding the residential or commercial properties and features of defoamers is necessary for manufacturers intending to enhance their procedures, enhance performance, and maintain the stability of their items (defoamers).
Trick Benefits of Defoamers
Making use of defoamers in producing procedures offers a variety of significant benefits that enhance functional efficiency and product top quality. Among the key advantages is the decrease of foam formation during manufacturing, which can obstruct machinery and interrupt operations. By lessening foam, defoamers make sure smoother procedures, resulting in lowered downtime and upkeep costs.
Furthermore, defoamers enhance item uniformity by protecting against air entrapment, which can compromise the stability of the last item. This is particularly important in sectors where visual appearance and structure are essential, such as in paints, finishings, and food items. Boosted item high quality not just fulfills customer expectations but also enhances brand name track record.
In addition, defoamers can aid in optimizing resource use. By improving the efficiency of basic material use, they add to set you back financial savings and lowered waste, straightening with sustainability objectives. Last but not least, the application of defoamers can bring about much shorter handling times, making it possible for suppliers to increase manufacturing ability without substantial capital expense - defoamers.
Applications in Various Industries
In producing processes throughout various sectors, the application of defoamers plays a vital function in enhancing efficiency and item top quality. These chemical additives are used in markets such as food and beverage, pharmaceuticals, and textiles to alleviate foam-related obstacles.
In the food and drink sector, defoamers are important during the fermentation process, protecting against foaming that can interrupt production and ruin the product's integrity. In the pharmaceutical industry, defoamers are made use of in the formula of liquid medications, making certain uniformity and security while lessening waste.
Textile manufacturing also takes advantage of defoamers, as they are used in coloring and completing processes to promote even circulation of dyes and chemicals. This application not only improves the final product's look yet additionally minimizes the quantity of water and energy taken in during production.
In addition, in the paper and pulp industry, defoamers assist maintain procedure efficiency by minimizing foam that can prevent machinery efficiency. Generally, the varied applications of defoamers across these industries highlight their relevance in enhancing production processes and supplying high-quality products.
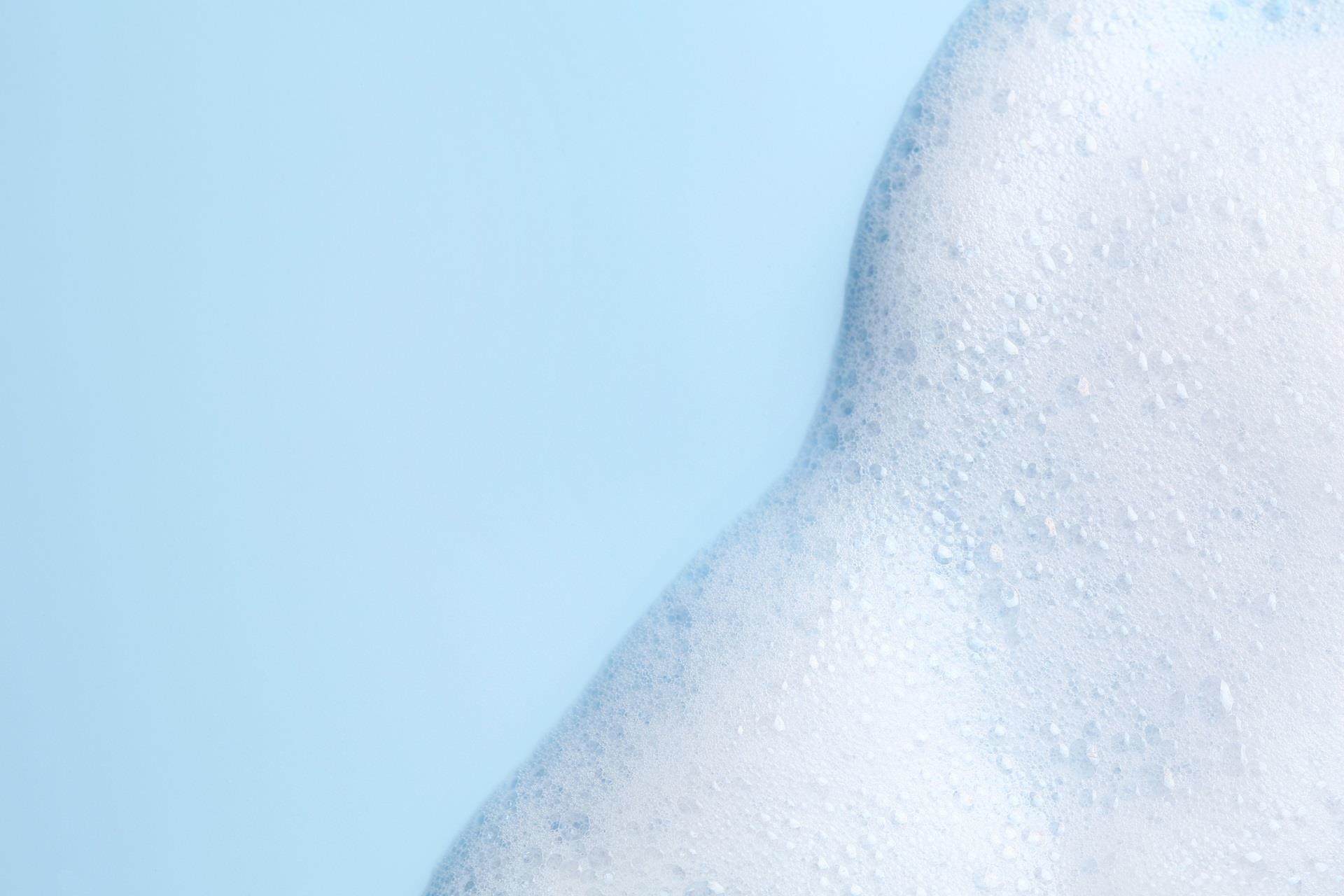
Choosing the Right Defoamer
Choosing an ideal defoamer is important for making the most of performance and quality in making procedures. The choice of defoamer depends upon different factors, including the details application, the kind of foam being created, and the formulation of the item being manufactured.
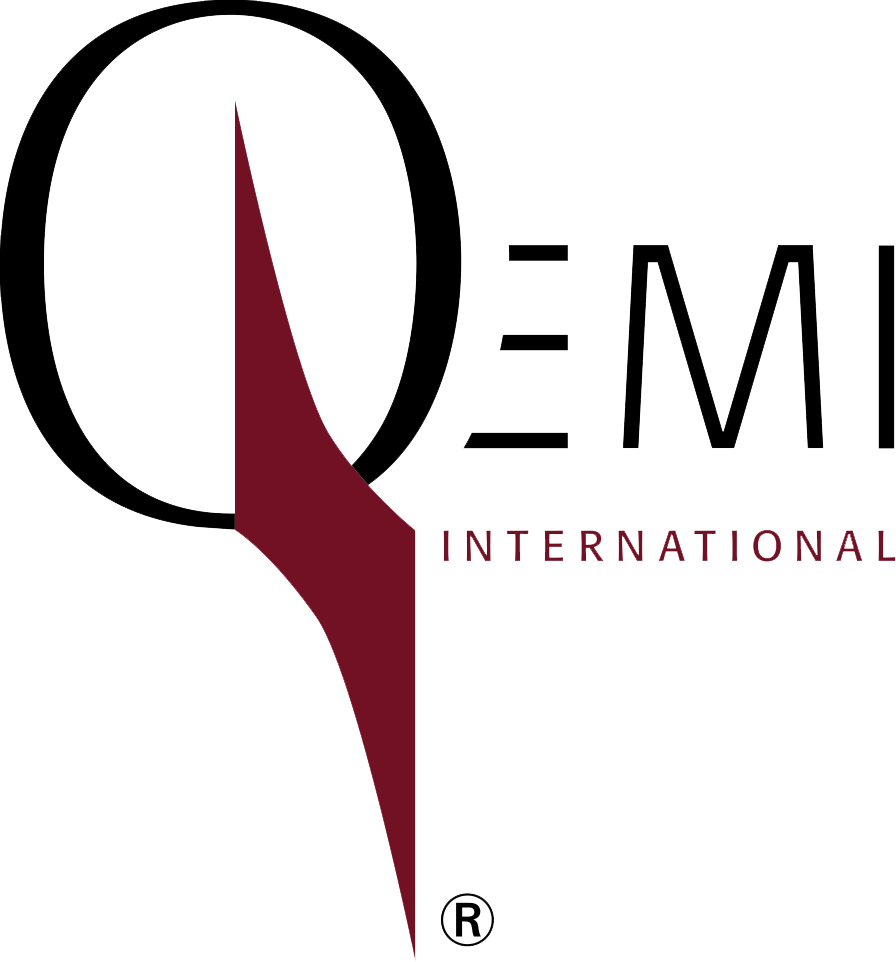
To start with, think about the chemical compatibility of the defoamer with other active ingredients in your solution. A defoamer that engages adversely with other elements can negatively impact item top quality. Additionally, the temperature and pH variety during handling are essential; some defoamers perform ideally under certain problems while coming to be inefficient in others.
Secondly, examine the defoamer's performance characteristics, such as its capacity to quickly decrease foam and its persistence during manufacturing. It is crucial to select an item that not only removes foam swiftly yet likewise maintains its effectiveness over time.
Lastly, take into consideration ecological and governing aspects, especially if your production process is subject to rigorous conformity standards. Selecting a naturally degradable or low-toxicity defoamer can assist meet sustainability goals while guaranteeing operational effectiveness. By attentively evaluating these requirements, suppliers can make educated choices that enhance performance and product honesty.
Ideal Practices for Application
Successful application of defoamers in producing procedures requires mindful preparation and adherence to ideal techniques. Picking the appropriate defoamer, as previously talked about, is vital; guarantee it is compatible with the products involved and resolves the determined lathering problems successfully.
Following, preserve clear interaction with all stakeholders, consisting of operators and quality assurance teams. Training sessions can help ensure that everybody understands the dosing treatments, prospective effect on item quality, and security factors to consider. Implementing a test stage can likewise be beneficial; screen performance carefully to gauge effectiveness and make needed changes.
In addition, normal testing and surveillance of foam degrees can provide valuable understandings right into the defoamer's performance in time. Adjusting dosages in feedback to changes in manufacturing variables will certainly help preserve optimum efficiency - defoamers. check my blog Lastly, documenting all processes and results promotes constant improvement, enabling fine-tuning of defoamer use and enhancing total performance in producing operations.
Final Thought
In recap, defoamers play an essential role in boosting efficiency within manufacturing and manufacturing processes. By reducing foam formation and assisting in bubble Clicking Here coalescence, defoamers add to improved item high quality, consistency, and functional effectiveness. Their application across various industries underscores their adaptability and value in enhancing resource usage and decreasing processing times. Ultimately, the strategic application of defoamers makes it possible for producers to boost production capacity effectively, consequently meeting customer assumptions and attaining price savings.
The benefits extend to product quality and cost savings, as defoamers help streamline processes.Defoamers play an important duty in numerous producing processes by effectively combating the formation of foam, which can impact and disrupt operations item high quality. Comprehending the properties and features of defoamers is crucial for makers aiming to optimize their procedures, improve productivity, and keep the honesty of their products.
Making use of defoamers in producing processes offers an array of considerable advantages that improve functional effectiveness and item high quality.Additionally, defoamers boost product uniformity by stopping air entrapment, which can compromise the honesty of link the final product.